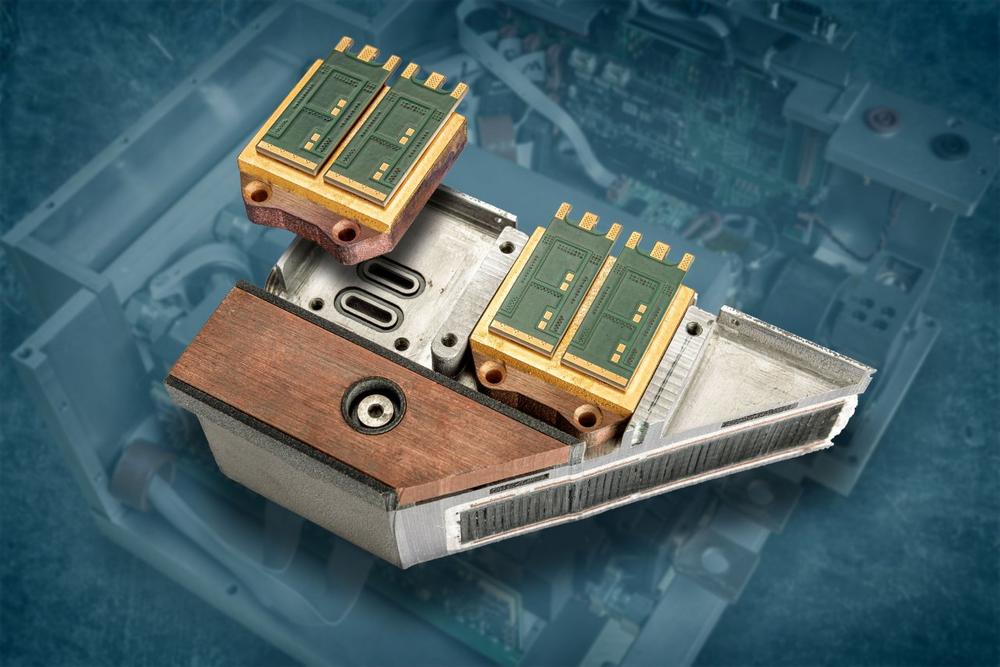
Um die Energie aus der Batterie auf die Straße zu bringen, brauchen die Motoren heutiger Elektroautos einen Wechselrichter. Er ist sozusagen das Umspannwerk im Auto. Der Wechselrichter wandelt den Gleichstrom aus der Batterie in das, was aktuelle Motoren antreibt: in Dreiphasenwechselstrom, landläufig auch als Drehstrom bekannt. Je höher die Leistung im Antriebsstrang, desto größer der Stromfluss. Damit wächst die Wahrscheinlichkeit von Wärmeverlusten. Minimiert wird dieser störende Nebeneffekt durch einen neuartigen Wandler, den das Fraunhofer IZM nun in Zusammenarbeit mit Porsche und Bosch entwickelt hat: der Dauerpower-Wechselrichter.
Der Name ist Programm, denn auch über lange Zeiträume stellt der Dauerpower-Wechselrichter knapp 600 Kilowatt Leistung bereit, was etwa 815 PS entspricht. Zum Vergleich: Das ist nicht nur gut anderthalbmal so viel, wie derzeit in einem 40-Tonnen-LKW üblich, es setzt vor allem neue Maßstäbe im Segment der elektrisch angetriebenen Sportwagen. Für kurzfristige Leistungsspitzen erreicht der Wechselrichter sogar Werte von 720 Kilowatt oder 979 PS. Um solche Energiemengen verarbeiten zu können, wurde bei der Entwicklung des Dauerpower-Moduls auf modernste Halbleitertechnik mit Siliziumkarbid-Transistoren (SiC) gesetzt und ein innovatives Kühlsystem entwickelt.
Hohe Effizienz und niedrige Induktivität dank Leiterplattenembedding
Die Basis für die herausragende Leistungsfähigkeit des Dauerpower-Wechselrichters bildet der Einsatz von Transistoren aus Siliziumkarbid (SiC). Ein großes Plus liegt in der geringeren Modulinduktivität von 1,1 Nanohenry– unter Modulen mit ähnlicher Stromleitfähigkeit ist das absolute Spitzenklasse. Dominik Seidenstücker, der federführend an dieser Entwicklung beteiligt war, erläutert weitere Vorteile: „Im Vergleich zu herkömmlichen Siliziumtransistoren zeichnen sich Siliziumkarbid-Halbleiter durch eine wesentlich höhere Temperaturbeständigkeit, geringere Halbleiterkapazitäten und einen reduzierten Durchlasswiderstand bei gleicher Halbleiterfläche aus. Daher bieten sie das Potenzial, Schalt- und Leitverluste erheblich zu reduzieren.“
Um das System besonders kompakt zu gestalten, wurden zudem DC-Link-Kondensatoren mit PolyCharge NanoLam-Technologie verwendet. Im Vergleich zu den üblichen Polypropylen-Kondensatoren bieten sie mehr als die doppelte Leistungsdichte. Durch ein spezielles Leiterplattenverfahren, bei dem die Halbleitermodule eingebettet werden, wird die Systemeffizienz weiter gesteigert. Dazu Dominik Seidenstücker: „Das Leiterplattenembedding ermöglicht uns, den Abstand zwischen den Hin- und Rückleitern zu verringern und so die Streuinduktivität zu reduzieren. Die geringere Streuinduktivität des Moduls führt dazu, dass wir schneller schalten können. Dies wiederum reduziert die Verluste im Halbleiter abermals.“ Außerdem erlaubt diese Technologie eine kostengünstige Massenproduktion. Das hochmoderne, auf SiC-Technologie basierende Design hält die Wärmeentwicklung in den 12 verbauten Halbleitermodulen auf niedrigem Niveau. Leitet der Dauerpower-Wechselrichter bei Bedarf besonders große Energiemengen zum Antriebsaggregat, sorgt ein raffiniertes Kühlsystem für viel Spielraum.
Hochmodernes Kühlsystem aus dem 3D-Drucker
Damit die Leistungselektronik auch unter Volllastbedingungen zuverlässig arbeiten kann, wurde ein Kühlsystem entwickelt, das im Wesentlichen auf zwei Teilen basiert: Zum einen wurde ein 3D-gedrucktes Kupferkühlelement entwickelt. „Wir haben uns für Kupfer entschieden, da Kupfer eine bessere thermische Leitfähigkeit hat als Aluminium und dadurch die Wärme besser spreizen kann,“ so Seidenstücker. Das Element ist optimal an die thermischen Anforderungen der Bauteile angepasst und sorgt für eine gleichmäßige Wärmeabfuhr. Durch den Einsatz von Silbersinterverbindungen werden die temperaturkritischen Komponenten direkt an das Kühlsystem angeschlossen, wodurch eine bestmögliche thermische Integration erreicht wird.
Weitergeleitet wird die Wärme an eine Wasserkühlung, die zweite Komponente des Kühlsystems. Sie wird im Aluminium-3D-Druck-Verfahren hergestellt und führt das Kühlwasser durch eine parallele Kühlstruktur, die den Druck im System optimal verteilt. Der Druckabfall ist mit nur 150 Millibar bei 10 Litern Kühlmittel pro Minute extrem gering – ein klarer Beweis für die hohe Effizienz der Kühltechnik. Selbst nach 15 Minuten Dauerlastbetrieb beträgt die Temperaturdifferenz zwischen Gehäuse und Kühlmedium weniger als 20 Kelvin. Am gekühlten Phasenausgang konnte eine maximale Temperaturerhöhung von nur 41 Kelvin gemessen werden. Dank dieser fortschrittlichen Kühltechnologie bleibt der Wechselrichter auch bei hoher Beanspruchung im Bereich optimaler Betriebstemperaturen. Salopp gesagt: Im Dauerpower bleibt selbst das Kühlsystem cool.
Maximale Leistungsdichte
Die einzelnen Baugruppen des Dauerpower-Wechselrichters sind also bestens aufeinander abgestimmt. Orchestriert wird ihr Zusammenspiel durch eine Software, die ebenfalls vom Fraunhofer IZM für das Projekt entwickelt wurde. Nicht zuletzt ermöglicht das smarte Design des Moduls ein Kraftpaket, das neue Maßstäbe in Sachen Leistungsdichte setzt: Mit 200 kVA pro Liter leistet der Wechselrichter das Zwei- bis Vierfache dessen, was in gängigen Elektroautos üblich ist. Das heutige Spitzensegment übertrifft er um ein Drittel. Hochleistungs-Elektrofahrzeuge können künftig also von deutlich kleineren Umrichtern mit mehr Leistung ins Rennen geschickt werden. Zudem bietet der Dauerpower-Wechselrichter eine hohe Modularität: Einzelne Komponenten können leichter ausgetauscht oder gewartet werden. Das spart Ressourcen und ermöglicht eine wesentlich längere Nutzungsdauer der Fahrzeuge.
Die Kombination aus modernster Halbleitertechnik, optimierter Kühlung und hoher Leistungsfähigkeit macht den Wechselrichter zu einem Schlüsselbaustein für die nächste Generation elektrischer Antriebe. Das Projekt trägt maßgeblich zur Weiterentwicklung der Elektromobilität bei und legt die Messlatte in Sachen Leistung, Effizienz und Nachhaltigkeit ein deutliches Stück höher.
Unterstützt wurde das Projekt vom Bundesministerium für Wirtschaft und Klimaschutz, durchgeführt wurde es in Zusammenarbeit mit der Porsche AG und der Robert Bosch GmbH.
Vom 6.-8. Mai stellt Dominik Seidenstücker den Dauerpower-Wechselrichter am Stand des Fraunhofer IZM (Halle 5, Stand 300) auf der PCIM Europe der Öffentlichkeit vor. Lassen Sie sich von unseren Wissenschaftlern die technischen Innovationen erläutern und werfen Sie einen Blick auf unseren zukunftsweisenden Antriebsumrichter mit seinen eingebetteten Leistungsmodulen und dem innovativen Zwischenkreiskondensator.
Weitere Informationen zu unserem Stand: https://www.izm.fraunhofer.de/de/news_events/events/pcim.html
Technische Daten
3-phasiger Antriebsumrichter
48 SiC-Halbleiter
ca. 3 l Volumen des Power Cores
800 bzw. 1200 V Basis
Dauerleistung von knapp 600 kW (835 V x 720 ARMS)
Spitzenleistung von 720 kW (800 V x 900 ARMS)
Leistungsdichte von 200 kVA pro Liter
Spitzen-Effizienz von 98,7 %
Das Fraunhofer IZM ist weltweit führend bei der Entwicklung und Zuverlässigkeitsbewertung von Technologien für die Aufbau- und Verbindungstechnik von zukünftiger Elektronik. Hierdurch entstehen Eigenschaften, die bislang eher untypisch für Mikroelektronik sind: zum Beispiel wird sie dehn- oder waschbar, hochtemperaturbeständig oder extrem formangepasst. Die Forschenden des Fraunhofer IZM setzen dabei ebenso Maßstäbe für die Umweltverträglichkeit von Elektronik.
Fraunhofer-Institut für Zuverlässigkeit und Mikrointegration IZM
Gustav-Meyer-Allee 25
13355 Berlin
Telefon: +49 (30) 46403-100
Telefax: +49 (30) 46403-111
http://www.izm.fraunhofer.de
Presseansprechpartner
Telefon: +49 (30) 46403-279
Fax: +49 (30) 46403-650
E-Mail: georg.weigelt@izm.fraunhofer.de
System Integration & Interconnection Technologies
Telefon: (030) 46403-7999
E-Mail: dominik.seidenstuecker@izm.fraunhofer.de