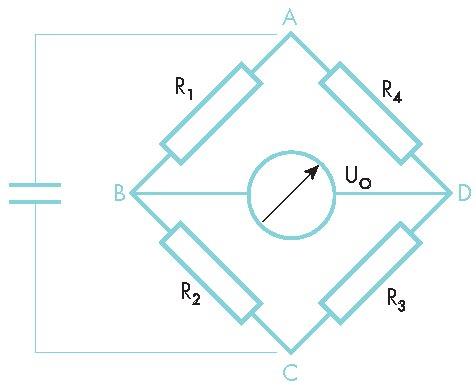
Drucksensoren messen jeweils Druckdifferenzen. Je nach Anwendung kann direkt die Differenz zwischen zwei Prozessdrücken interessieren. Häufig wird aber auch ein Prozessdruck relativ zum atmosphärischen Druck gemessen. Der atmosphärische Druck variiert zwar leicht in Abhängigkeit unterschiedlicher Parameter wie geografischer Position und Wetter, was aber in vielen Situation vernachlässigbar ist oder sich sogar stabilisierend auf den Prozess auswirkt. Wenn ein immergleicher Referenzdruck benötigt wird, kommt in den meisten Fällen das möglichst absolute Vakuum als Referenz zum Einsatz. Dies ist zum Beispiel beim Barometer der Fall, mit dessen Hilfe Veränderungen des atmosphärischen Druckes absolut gemessen werden können.
In den allermeisten Fällen wird für die Messung dieser Druckdifferenzen eine Membrane verwendet. Diese kann aus unterschiedlichsten Materialien wie Stahl, Keramik oder Silizium gefertigt sein. Die Druckdifferenz führt zu einer Auslenkung dieser Membran, deren Magnitude wiederum gemessen werden muss. Wenn Beschaffenheit und Auslenkung einer Membran bekannt sind kann davon die Druckdifferenz abgeleitet werden.
Eine häufige Messmethode um diese Auslenkung zu messen sind Widerstände die durch die Auslenkung der Membran ihren Wert verändern. Um leichte Änderungen des Widerstandswertes mehrerer Widerstände zuverlässig in ein Spannungssignal umzuwandeln, bietet sich die Wheatstonebrücke an. In dieser Anordnung bilden R1 und R2 den einen Spannungsteiler, R3 und R4 den anderen. Die Differenz der Ausgangsspannungen der beiden Spannungsteiler entspricht dem Ausgangssignal der gesamten Messbrücke. Die Widerstände werden nun so angeordnet, dass R1 und R3 ihren Widerstandswert bei Druckbeaufschlagung verringern und R2 und R4 den Ihren
erhöhen. Die Brücke wird über eine elektrische Spannung zwischen A und C versorgt. Wenn der Sensor nun mit Druck beaufschlagt wird, resultiert dies in einem steigenden Pegel bei B und einem sinkenden Pegel bei D, und damit einer positiven Ausgangsspannung zwischen B und D.
Bei einer komplett unbelasteten Membran wird in den meisten Fällen ein Ausgangssignal von 0mV angestrebt, also R1=R2=R3=R4=R. Dieser Wert R sei beispielhaft bei 3500Ohm angesetzt, während die Versorgungsspannung bei 5V liege. Damit liegen die Pegel von B und D beide bei 2.5V. Unter maximaler Belastung sei die Widerstandsdifferenz 30Ohm, also R1=R3=3530, R2=R4= 3470. Damit steigt der Pegel bei B auf 2.521V, bei D sinkt er auf 2.479V. Daraus ergibt sich zwischen B und D ein Ausgangssignal von 42.1mV bei maximaler Druckbeaufschlagung. Dieses Signal kann dann verstärkt und weiter konditioniert werden, um die maximale Genauigkeit zu erreichen.
Bei Piezoresistiven MEMS Drucksensoren besteht die Membrane aus Silizium. Die wesentlichsten Parameter der Membrane sind deren Fläche und Dicke. Dabei gilt, dass für die Messung kleinerer Druckdifferenzen grundsätzlich grössere und dünnere Membranen benötigt werden.
Die Messung der Auslenkung geschieht, wie der Name sagt, mittels Piezowiderständen. Piezowiderstände zeichnen sich dadurch aus, dass sie unter mechanischer Spannung ihren Widerstand ändern. Solche Piezowiderstände werden am Perimeter der Membran platziert, wo aufgrund der unterschiedlichen Steifigkeit der Membran zum Rahmen um die Membran die mechanische Spannung am grössten ist. Im Kontext von Drucksensormembranen handelt es sich bei der auftretenden mechanischen Spannung immer um eine Zugspannung. Trotzdem kann diese Zugspannung, je nachdem ob ein Piezowiderstand parallel oder senkrecht zur Membrankante angeordnet ist, in einem verringerten- oder einem erhöhten Widerstand resultieren. Dies kann analog zum Einfluss der Geometrie eines Leiters auf dessen elektrischen Widerstand verstanden werden. Dabei entspricht die auf einen parallel zur Membrankante angeordneten Piezowiderstand ausgeübte mechanische Zugspannung einer «Vergrösserung» des Leiterquerschnittes und damit einer Verringerung des Widerstandes. Bei einem senkrecht angeordneten Piezowiderstand wiederum entspricht die mechanische Zugspannung einer «Verlängerung» des Leiters und geht damit mit einer Vergrösserung des Widerstandes einher. Bei dieser Analogie ist wichtig zu betonen, dass diese lediglich der Veranschaulichung des piezoelektrischen Effektes dient. Die Piezowiderstände verformen sich nicht.
Vom rohen Wafer zum MEMS Chip
Ein grosser Teil der Prozesse, die für die Herstellung von MEMS-Bauteilen verwendet werden, kommen aus der klassischen Halbleiterindustrie. Dies sind im wesentlichen unterschiedliche Verfahren für Materialabscheidung, Fotolithografie, Ionenimplantation und Ätzen. Dazu kommen unterschiedliche Reinigungsverfahren, um die Wafer von Partikeln, Reaktionsprodukten und anderem zu befreien. Insbesondere bei den Ätzverfahren kommen zusätzliche Prozesse hinzu, die nur in der Produktion von MEMS-Bauteilen verwendet wird.
Ein wesentlicher MEMS Prozess ist das Abscheiden von Dünnfilmen auf dem Wafer. Damit können unterschiedliche Materialien auf den Wafer aufgebracht werden. Dies können zum Beispiel Metalle sein, mit denen elektrische Verbindungen auf dem Chip erzeugt werden. Ein Beispiel für Abscheidungsverfahren ist die chemische Gasphasen-abscheidung. Hierbei werden reaktive Gase auf den Wafer diffundiert und von diesem absorbiert. Es folgt eine Reaktion auf der Waferoberfläche, bei der das gewünschte Material in einer festen Phase ausfällt und sich als dünne Schicht von 1-10nm auf der Waferoberfläche festsetzt. Nebenprodukte der chemischen Reaktion werden desorbiert und vom Wafer weg transportiert.
Um die so erzeugen Dünnschichten sinnvoll nutzen zu können, müssen sie strukturiert werden, was über die folgenden Prozessschritte gemacht werden kann.
Ein weiter wichtiger Schritt ist die Fotolithografie. Die Fotolithografie ermöglicht das selektive Ätzen in einem nachfolgenden Schritt, und damit die Strukturierung von Materialien auf dem Wafer. Dafür wird auf den Wafer zuerst, häufig mittels Rotationsbeschichtung, ein Fotolack aufgebracht. Dieser wird dann selektiv durch eine optische Maske belichtet. Durch diese Belichtung verändern sich die chemischen Eigenschaften des Lackes dahingehend, dass im nächsten Schritt, bei Positivlack, ausschliesslich die chemisch veränderten Regionen des Lackes entfernt werden können, bzw. bei Negativlack ausschliesslich die nicht veränderten Regionen des Lackes entfernt werden können.
Als Folge der Lithografie sind durch die optische Maske definierte Bereiche des Wafers exponiert, während andere Bereiche durch Fotolack geschützt sind. Dieser Zustand kann genutzt werden, um in den Wafer selektiv in diesen exponierten Regionen zu bearbeiten, zum Beispiel durch Ätzen oder durch Ionenimplantation.
Bei der Ionenimplantation werden Fremdatome in die Oberfläche des Wafers eingebracht bzw. dotiert. Dafür werden Ionen in einem Hochvakuum auf den Wafer beschleunigt. Vor diesem Schritt wird der Wafer in den meisten Fällen maskiert, um diese Fremdatome nur lokal einzubringen. Durch die Fremdatome werden meist die elektrischen Eigenschaften des dotierten Materials manipuliert. Beispielsweise kann die Leitfähigkeit von Silizium
verändert und damit ein definierter Widerstand gefertigt werden. Die für den Drucksensor essenziellen Piezowiederstände, die die Spannung der Membran messen, werden auf diese Weise hergestellt.
Alternativ zur Ionenimplantation kann ein maskierter Wafer auch selektiv geätzt werden. Die Ätzverfahren unterteilen sich im Wesentlichen in Nassätzverfahren, bei denen flüssige Ätzlösungen zum Einsatz kommen, und Trockenätzverfahren, bei denen mittels Plasma
geätzt wird. Typischerweise werden Ätzschritte eingesetzt um Materialien auf dem Wafer zu strukturieren, oder um Hilfsschichten zu entfernen. Beim Strukturieren werden typischerweise die Bereiche einer Dünnschicht weggeätzt, die nicht durch Fotolack geschützt sind.
Nach der Strukturierung muss die Hilfsschicht, der Fotolack, weggeätzt werden.
Bei beiden diesen Schritten ist die Ätzselektivität von hoher Bedeutung. Sei beispielsweise mittels Gasphasenabscheidung eine Aluminiumschicht direkt auf einen Siliziumwafer aufgebracht worden. Die Aluminiumschicht sei mittels Fotolithografie mit Fotolack maskiert worden. Um die Aluminiumschicht zu strukturieren, ist ein Ätzmedium gewünscht, welches Aluminium deutlich stärker angreift als den Fotolack und das Silizium, da der Fotolack die zu erhaltenden Regionen der Aluminiumschicht schützen soll und das Silizium unter dem Aluminium nicht angegriffen werden soll. Beim Wegätzen des Fotolackes ist wiederum ein Ätzmedium erwünscht, welches den Fotolack deutlich stärker angreift, als das jetzt exponierte Silizium sowie das Aluminium, das während des Ätzschritts unter dem Fotolack zum Vorschein kommt.
Ein aussergewöhnliches Ätzverfahren ist das Deep reactive ion etching (DRIE), mit dessen Hilfe tiefe Strukturen möglichst orthogonal in das Wafersubstrat geätzt werden. Im ersten Schritt wird der Wafer maskiert, sodass nur die zu ätzenden Regionen exponiert sind.
Danach startet der erste Ätzschritt. Dafür werden Ionen aus einem SF6-Plasma in einem elektrischen Feld beschleunigt. Damit wird Material primär orthogonal zur Waferoberfläche abgetragen. Da dieser Ätzschritt aber nicht 100% orthogonal fortschreitet, wird nach kurzer Zeit der Ätzschritt gestoppt und eine Passivierungsschicht über den gesamten Wafer appliziert. Dann wird wiederum geätzt wie zuvor, wobei zuerst die Passivierungsschicht auf dem Grabenboden weggeätzt wird und dann der Graben tiefer geätzt wird.
Diese beiden Schritte werden abwechslungsweise so lange wiederholt, bis die gewünschte Grabentiefe erreicht wird. Das Resultat ist eine Mikrostruktur mit Wänden, die weitgehend orthogonal zur Waferobefläche angeordnet sind. Dabei weisen diese eine charakteristische wellige Oberfläche auf.
Im Kontext von Drucksensoren hat das DRIE Verfahren im Gegensatz zum klassischen Nassätzten mit Kaliumhydroxid (KOH) Vor- und Nachteile:
Bei DRIE muss jeder Wafer einzeln prozessiert werden, was zu höheren Kosten pro Wafer führt als beim Nassätzen, bei dem ganze Waferlots zeitgleich geätzt werden können.
Weiter kann bei gleichbleibender Membrangrösse aufgrund der mittels DRIE gefertigten senkrechten Wände unter der Membran die Grösse des ganzen Druckchips reduziert werden, was zu tieferen Kosten pro Chip führt.
Ein Nachteil von KOH ist, dass nassgeätzte Strukturen zwingend rechteckig sein müssen, da KOH anisotropisch ätzt, während DRIE das orthogonale Ätzen beliebiger Geometrien zulässt. Mit einer angepassten Geomtrie kann beispielsweise die mechanische Stresskonzentration optimiert werden.
Ein weiterer Vorteil des DRIE Ätzens, der insbesondere bei Niederdrucksensoren zum Tragen kommt, ist die Beschaffenheit des Ätzstopps. Im falle eines Drucksensors ist dies die Rückseite der Membran. Bei KOH geätzten Produkten ist dieser Ätzstopp uneben. Mit DRIE kann eine deutlich weniger unebene Oberfläche gefertigt werden. Die Ebenheit der Rückseite der Membran ist bei Niederdrucksensoren besonders wichtig, da die Membran bei diesen besonders dünn ist. Die selbe Unebenheit bedeutet bei einer dünneren Membran aber einer deutlich grösseren Abweichung von der Solldicke.
Absolut oder differenziell?
Je nach Anwendung interessiert eine absolute- oder eine relative bzw. differenzielle Druckmessung. Für absolute Drucksensoren muss auf der einen Seite der Membran ein Vakuum erzeugt und gehalten werden, was am einfachsten über Waferbonding gelöst wird.
Beim Waferbonden werden zwei Wafer flächig miteinander verbunden. Bei MEMS-Drucksensoren handelt es sich beim einen Wafer jeweils um einen wie oben be-schriebenen Siliziumwafer. Beim anderen Wafer kann es sich ebenfalls um einen Silizium-, häufiger aber um einen Glaswafer, handeln.
Es gibt unterschiedliche Waferbondverfahren, wobei bei MEMS-Drucksensoren das anodische Bonden am weitesten verbreitet ist. Die beiden polierten und behandelten Wafer bilden dabei unter Temperatur und elektrischer Spannung eine starke Verbindung.
Waferbonden kann eingesetzt werden, um Absolutdrucksensor zu fertigen. Dafür muss der Druck auf einer Seite der Membran konstant gehalten werden. Dies gelingt, in dem unter Vakuum-umgebung ein Glaswafer auf die Rückseite eines MEMS Drucksensorwafers gebondet wird. Damit kann jeder von vorne beaufschlagte Druck relativ zum auf der Rückseite der Membran herrschenden Vakuum und damit absolut gemessen werden.
Vom MEMS Chip zum Drucksensor
Piezoresistive MEMS Drucksensoren wandeln eine mechanische Spannung in ein elektrisches Signal um. Um ein möglichst genaues Signal zu erhalten, soll die gewandelte mechanische Spannung möglichst ausschliesslich durch den beaufschlagten Druck verursacht werden. Der Einfluss anderer Quellen von mechanischen Spannungen soll deshalb auf ein Minimum reduziert werden.
Die wichtigste unerwünschte Quelle von solchen Spannungen ist die Temperatur. Da jedes Material eine unterschiedliche thermische Expansion aufweist, führen Temperaturänderungen zu ungleichmässigen Ausdehnungen bzw. Kontraktionen, was wiederum zu mechanischen Spannungen führt. Diese Effekte werden natürlich beim Design eines MEMS-Chips berücksichtigt. Zum Beispiel werden kritische Strukturen möglichst symmetrisch aufgebaut, um einen Biegeeffekt im Stile eines Bimetalls zu verhindern. Wo möglich werden aber direkt Materialien mit möglichst ähnlichen thermischen Eigenschaften gewählt.
Nicht nur beim Design des Chips ist es wichtig, solche Effekte zu beachten. Auch bei der mechanischen Verbindung zwischen dem Druckchip und dem Gehäuse eines Drucksensors, Die-Attach genannt, ist darauf zu achten. Je nach Gehäusematerial ist die Differenz der thermischen Expansion zwischen Chip und Gehäuse erheblich. Wird beispielsweise ein Siliziumchip mit einer thermischen Expansion von 2.56×10-6/K direkt in ein Kunststoffgehäuse mit einer thermischen Expansion von 26×10-6/K montiert, werden bei Temperaturänderungen signifikante Spannungen in den Chip übertragen.
Je niedriger der nominelle Druckmessbereich des Chips ist, desto empfindlicher ist der Chip auch auf solche Spannungen. Insbesondere für das Montieren von Niederdruckchips ist es deshalb zu empfehlen, Tests mit unterschiedlichen Klebstoffen durchzuführen. Auch die unterschiedlichen Methoden des Applizierens des Klebstoffes sind zu evaluieren.
Die wichtigsten Eigenschaften des Die-Attach sind dessen Festigkeit, der Abstand zwischen Siliziumchip und Gehäuse sowie die Kontamination der Wände des Chips. Bezüglich Festigkeit ist ein möglichst weicher Die-Attach anzustreben, da dieser so möglichst viele Spannungen absorbieren kann. Der Abstand zwischen Chip und Gehäuse soll ausreichend gross sein, wiederum um die Absorption von Spannungen zu ermöglichen. Dabei soll der Die-Attach aber möglichst wenig an den Wänden des Siliziumchips hochwandern, da damit wiederum die Entkopplung gemindert wird.
Um die Aufgabe des Die-Attach zu vereinfachen kann ein Rückseitenglas an den Sensorchips implementiert werden.
Dies geschieht wie bei Absolutdrucksensoren mittels Waferbonden. Glas verfügt über eine relativ ähnliche thermische Expansion wie Silizium (3.2×10-6/K vs. 2.56×10-6/K). Damit entstehen nur minimale temperaturbedingte Spannung zwischen Glas und Silizium, während das Glas Spannungen die vom Sensorgehäuse kommen weitgehend absorbieren kann. Dies kann den Die-Attach Prozess massiv vereinfachen, da ein solcher Chip mit Rückseitenglas recht einfach geklebt werden kann.
Glas hat allerdings den Nachteil, dass es sich um ein amorphes Material handelt. Glas ist damit, im Gegensatz zu Silizium, nicht kristallin, was bedeutet, dass sich Glas langfristig geometrisch verändern bzw. «fliessen» kann. Hierbei geht es um Zeiträume von Monaten und Jahren, über die sich das Glas verändert und damit eine mechanische Spannung im Siliziumchip verursacht. Dies ist im Sensorsignal dann als Zero-Offset Drift sichtbar. Dieser Effekt macht sich wiederum besonders bei Niederdrucksensoren bemerkbar, während er bei höheren Drücken meist vernachlässigbar ist. Für die langfristig beste Niederdruck-performance ist also ein mittels gut implementiertem Die-Attach Prozess befestigter Siliziumchip einem Chip mit Rückseitenglas vorzuziehen.
Welche Sensorkonstruktion und Technologie für den DIE Attach die Beste ist hängt von der Applikation ab. Je nach Anwendung, Medium und Druckbereich kann dies variieren. Alle diese Faktoren müssen zusammen betrachtet werden, um den besten Sensor für eine bestimmte Anwendung zu designen und zu produzieren.
Persönliche Betreuung, rasche Reaktionszeiten und individuelle Lösungen zeichnen Angst+Pfister Sensors and Power seit über 30 Jahren aus. In unserem breiten und tiefen Sortiment an Sensoren, Stromversorgungen und elektronischen Komponenten finden die Kunden die richtigen Komponenten für jeden ihrer speziellen Anwendungsbereiche. Je nachdem liefert die Angst+Pfister Sensors and Power den Kunden Standardprodukte, modifizierte Standardprodukte oder auch individuelle Anfertigungen. Angst+Pfister Sensors and Power arbeitet nur mit ausgewählten und renommierten Partnern zusammen, die hohen Ansprüche an Ausfallsicherheit, Langlebigkeit, Preis-Leistungs-Verhältnis und Qualität teilen. Zusätzlich ergänzen die Herstellung und der Vertrieb ausgewählter eigener Angst+Pfister Sensors and Power Produkte das breite Portfolio.
So lässt Angst+Pfister Sensors and Power die Kunden bei der Entwicklung nicht alleine, sondern sucht für jede Anwendung die beste Lösung. Die Spezialisten haben ein tiefes technisches Verständnis und stehen während der Entwicklungsphase zur Seite. Die Angst+Pfister Sensors and Power ist ein eigenständig operierendes Unternehmen der Angst+Pfister Gruppe und ist für Kunden in ganz Europa und Übersee tätig. Mit der Übernahme von IS-LINE durch die Angst+Pfister Gruppe im Jahr 2017 kann die Angst+Pfister Sensors and Power für die Kunden durch technisch kompetente Beratung und einem nochmals erweiterten Portfolio im Bereich Sensorik und Leistungselektronik, einen noch größeren Mehrwert generieren. Gemeinsam gehört die Angst+Pfister Sensors and Power damit zu einem weltweiten Netzwerk mit über 1 000 Mitarbeitern und 60 000 zufriedenen Kunden.
Angst+Pfister Sensors and Power AG
Thurgauerstrasse 66
CH8050 Zürich
Telefon: +41 (44) 87735-00
Telefax: +41 (44) 87735-25
http://sensorsandpower.angst-pfister.com
Marketing Manager
Telefon: +41 (44) 877 35 26
Fax: +41 (44) 8773525
E-Mail: yun.xu@angst-pfister.com