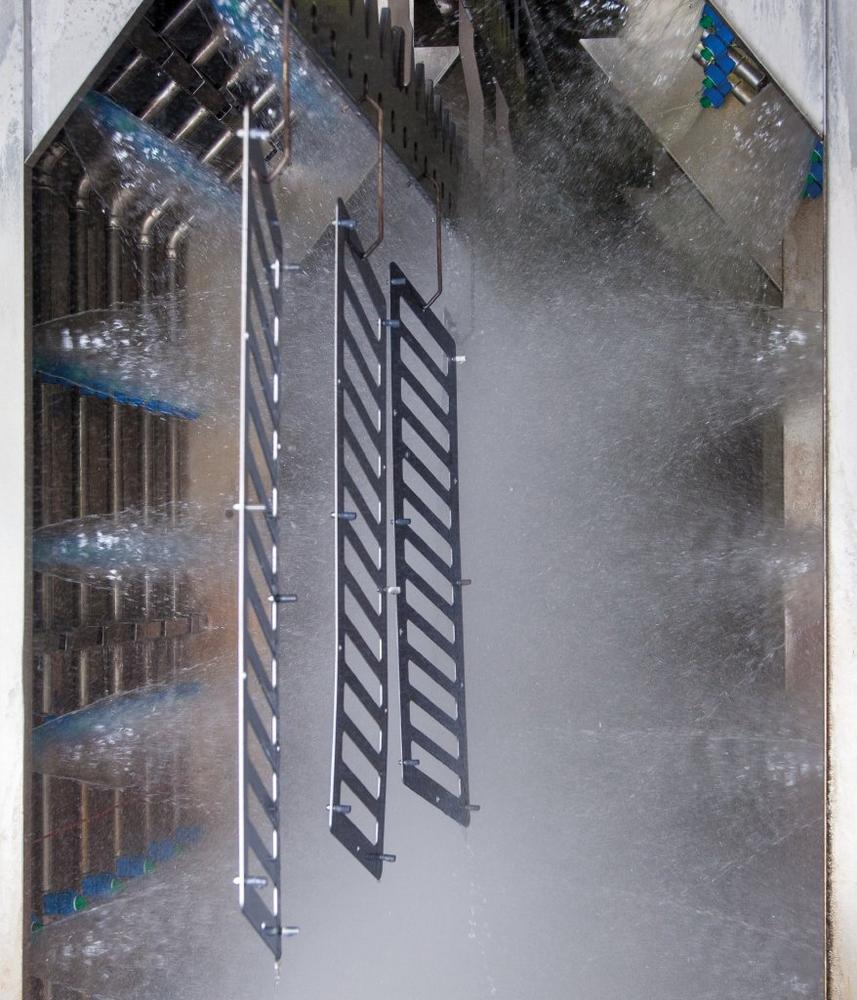
Nachdem diese Innovationsziele erreicht waren und sich etabliert hatten richtete sich der Fokus auf die Optimierung der Prozesskosten, um den Anwender im globalen Wettbewerb bestehen zu lassen. Somit bedeutet Nachhaltigkeit in der chemischen Oberflächentechnik heute kostenoptimierte Prozesse, die chemische Produkte umfassen, deren Anwendungsqualität hoch und deren Gefährdungspotential niedrig ist.
Ein gutes Beispiel für das oben Gesagte ist die Anwendung der Niedrigtemperatur-Zinkphosphatierung in Verbindung mit einer automatisierten Prozesskontrolle.
Problem: Phosphatschlamm
Die Zinkphosphatierung mit anschließender KTL-Beschichtung ist nach wie vor das Standardverfahren zur Erfüllung hoher Qualitätsanforderungen z.B. in der Automobilindustrie oder im Landmaschinenbereich. Die chemisch mit der Substratoberfläche verbundene Zinkphosphatschicht bietet durch ihre gegenüber dem Grundmetall deutlich vergrößerte Oberfläche viel mehr Verankerungspunkte für den Lack, d.h. die adhäsive Bindung der Lackbeschichtung an den Untergrund steigert sich erheblich.
Systembedingt entsteht bei der Zinkphosphatierung allerdings Phosphatschlamm, der dem System möglichst kontinuierlich z.B. durch eine Teilstrom-Filtration über eine Plattenfilterpresse entzogen werden muss. In der Installation verbleibender Schlamm lagert sich bevorzugt in horizontalen, strömungsberuhigten Zonen ab und muss teils aufwendig chemisch und / oder mechanisch entfernt werden („Bergmännischer Abbau").
Es lag also nahe ein System zu entwickeln, das anstelle von 45 – 50°C Anwendungstemperatur bei den zur Verfügung stehenden Behandlungszeiten auch bei 35°C arbeitet. Hierbei darf sich jedoch das einer modernen Trikation-Niedrigzink-Phosphatierung innewohnende ausgewogene Verhältnis der Konzentration der Kationen Zink, Nickel und Mangan untereinander und im Verhältnis zu den Haupt-Anionen Nitrat und Phosphat nicht ändern.
Erreicht wird eine ordnungsgemäße Schichtbildung bei Tauchprozessen durch die Verwendung eines Zinkphosphat-basierten Aktivierungsmittels und eine speziell abgestimmte Formulierung des Phosphatierprozesses. Neben der Einsparung an Heizenergie von 25 bis 30% und der damit verbundenen Verringerung des CO2-Footprints erzeugt das System um etwa 25% weniger und weicheren Phosphatschlamm, der sich einfacher entfernen lässt. Daneben wird zwischen 8 und 12 % weniger Phosphatier-Ergänzungslösung benötigt, was einen deutlichen Beitrag zur Ressourcenschonung darstellt.
Konstante Parameter dank automatisierter Prozesskontrolle
Schlussendlich sorgt der Einsatz einer automatischen Prozesskontrolle dafür, dass wichtige Prozess-Parameter konstant gehalten werden und das System nur um sehr kleine Konzentrationsamplituden schwingt. Das verringert Blindverbräuche z.B. beim Beschleuniger und die damit verbundenen unnötigen Kosten. Ferner bietet ein solches System die Möglichkeit der Prozessverknüpfung: Eine „denkende“ Dosierpumpe gibt ein Signal ins Chemikalienlager, dass ein neues Gebinde einer bestimmten Prozesskomponente benötigt wird. Damit können Supply Chain-Abläufe optimiert werden, kostenträchtige Sonderlieferungen werden weniger.
Ein automatisierter Regelkreis sieht z.B. so aus, dass ein Sensor kontinuierlich die elektrische Leitfähigkeit des Aktivierungsbades sowie den pH-Wert misst. Wird ein in der Steuereinheit programmierter pH-Grenzwert unterschritten, wird eine Dosierpumpe angesteuert, die einen pH-Regulator direkt aus dem Liefergebinde ins Bad pumpt. Ist der obere Sollwert erreicht, wird die Pumpe automatisch abgestellt.
Die Komponenten für eine automatische Prozesskontrolle sind, was die Beschaffungskosten betrifft, durchaus erschwinglich: Eine zentrale Steuereinheit mit 8 Eingängen für Messfühler wie elektrische Leitfähigkeit und 8 Ausgängen zur Ansteuerung von Dosierpumpen oder Ventilen ist bereits für ca. 4.000 Euro zu bekommen.
Insgesamt hat die chemische Oberflächentechnik die Herausforderungen im Hinblick auf Nachhaltigkeit erkannt und weiß sie auch zu meistern.
Autor: Dr. Ulrich Hönig – Head of Global Business Unit Pretreatment
Chemische Werke Kluthe GmbH
Gottlieb-Daimler-Str. 12
69115 Heidelberg
Telefon: +49 (6221) 53010
Telefax: +49 (6221) 5301130
http://kluthe.com
Global Corporate Communications
E-Mail: l.pleli@kluthe.com