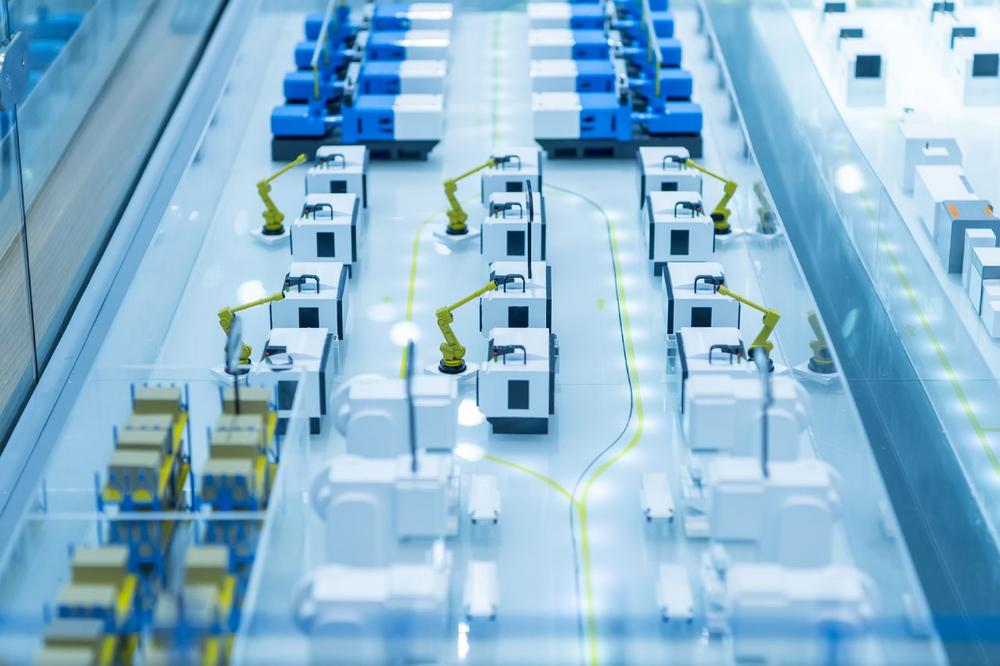
Die vorliegenden Ausführungen befassen sich damit, wie der Weg zur autonomen Fertigung typischerweise aussieht und welche Methoden und Ansätze sich in der Praxis bereits bewährt haben.
Ein Überblick über die Produktionssysteme im Kontext von Industrie 4.0
Wenn man das Konzept Industrie 4.0 genau verstehen will, muss man sich zunächst fragen, wie die neuen Produktionssysteme eigentlich entstanden sind und was bisher unternommen wurde, um Durchsatz und Effizienz in einer Fertigung zu steigern.
Ein erster Schritt in Richtung autonome Fertigung wurde mit der robotergestützten Prozessautomatisierung (RPA) unternommen. Dabei werden sich wiederholende Arbeitsschritte automatisiert, um die Durchsatzrate zu verbessern. Interessant ist, dass dieser Automatisierungsschritt keineswegs zu Qualitätssteigerungen, sondern lediglich zu einer Verfestigung bestehender Abläufe führt, denn schließlich werden dabei repetitive Vorgänge bis ins letzte Detail wiederholt¤ Mit der robotergestützten Prozessautomatisierung werden folglich zwar einerseits zehnmal so viele gute Teile produziert, andererseits steigt jedoch gleichzeitig auch die Fehlerquote. Wurden bislang bei einem bestimmten Teilprozess derzeit beispielsweise 1.000 fehlerhafte Teile produziert, sind es mit der RPA 10.000. Mit anderen Worten: Die Durchsatzrate steigt, was sehr zu begrüßen ist, nicht aber die Produktqualität.
Im nächsten Schritt rückten die Hersteller von diesem einfachen Automatisierungskonzept ab und bezogen alle Prozessdaten stärker in die Planung und Programmierung ihrer Produktionssysteme ein. So konnten Produktionsabläufe durch den Rückgriff auf gesammelte Datensätze, die Nutzung Speicherprogrammierbarer Steuerungen (SPS) usw. sehr viel genauer analysiert werden. Dies führt dazu, dass die Abläufe genauer überwacht werden können, wodurch wiederum weniger unterschiedliche Fehler auftreten und die Anzahl der Fehler insgesamt sinkt. Die Arbeit des Maschinenbedieners wird dadurch jedoch sehr anspruchsvoll, da er immer noch die letzte Kontrollinstanz ist.
Weitere Verbesserungen lassen sich durch eine Beschleunigung dieser Automatisierungsprozesse erreichen. Zwar setzt dies ein tiefes Verständnis der gesamten Produktionsabläufe voraus, doch kommt man damit dem Ziel der vollständig autonomen Fertigung deutlich näher. Produktionssysteme müssen so flexibel gestaltet sein, dass Änderungen an einzelnen Teilschritten vorgenommen werden können, ohne dass dies zu Lasten der Qualität des Endprodukts ginge.
Ohne Zweifel werden die Produktionssysteme im Kontext von Industrie 4¤0 in Zukunft immer flexibler. Bereits jetzt ist die Künstliche Intelligenz (KI) so weit entwickelt, dass Daten auch ohne menschliches Eingreifen vorausschauend, also noch schneller als in Echtzeit, korrigiert werden können, damit in bester Qualität, aber gleichzeitig zu möglichst niedrigen Kosten produziert werden kann.
Aktueller Stand der autonomen FertigungDas Ziel der vollständig autonomen Fertigung ist in der Regel nur über etliche Umwege zu erreichen. Denn schließlich ist die autonome Produktionsanlage keine einfache Maschine, die sich mit einem einzigen Knopfdruck einschalten ließe. Wie oben bereits erläutert, muss das KI-System einen Überblick über den gesamten Produktionsprozess behalten und den Mitarbeitern einer Produktionsanlage Vorschläge unterbreiten können, wie sich die Qualität weiter verbessern ließe. Nur so kann bei unterschiedlichsten Ausgangswerkstoffen und Aufgaben ein qualitativ hochwertiges Ergebnis erreicht und damit das wirtschaftliche Risiko der Fertigung reduziert werden. Ein geringerer Ausschuss führt zu einer Vergrößerung der Produktionskapazitäten sowie zu einer Zunahme an qualitativ hochwertigen Teilen. Letztlich lässt sich durch den Einsatz von KI also die Effizienz ganzer Produktionssysteme steigern.
In den meisten Fertigungsstätten wird heute im Laufe des Produktionsvorgangs eine Fülle an Daten erhoben und an die Konstruktions- oder Produktionsteams übermittelt. Ob sich diese Daten für eine Optimierung und Verbesserung der Produktionssysteme nutzen lassen, hängt immer noch ganz wesentlich vom Forschergeist der zuständigen Mitarbeiter ab. Eine ganzheitliche Betrachtung oder Nutzung der Daten, die den gesamten Produktionsprozess im Blick hätte, erfolgt in der Regel nicht.
Zudem wird die Analyse und Auswertung der erhobenen Daten häufig durch die Komplexität der Produktionssysteme erschwert. Mit den klassischen Arbeitsmethoden eines Ingenieurs lassen sich die technischen Vorgänge meist nicht genau abbilden. Ein Modell, mit dem sich ein Werkstoff vom Anfang einer Produktionskette bis hin zu dessen Ende genau verfolgen ließe, wäre so vielschichtig und umfangreich, dass die üblicherweise verwendeten Analysemethoden an ihre Grenzen stoßen würden. Auch die Rückverfolgbarkeit eines Bauteils ließe sich aufgrund der Komplexität der Produktionsvorgänge so kaum erreichen. Nur wenn ein Produktionssystem immer wieder Proben entnehmen und dadurch den Weg jeder einzelnen Komponente aufzeichnen würde, wären die komplexen Produktionsvorgänge für den Menschen noch in einzelnen Schritten nachvollziehbar.
Die Lösung für dieses vielschichtige Problem ist ein spezielles Prozessleitsystem EES (Expert Execution System). Mit diesem haben Hersteller gleichzeitig den Anfang und das Ende eines Produktionsprozesses im Blick, ohne jeden Produktionsschritt einzeln nachverfolgen zu müssen. Auf diese Weise wird das Problem etwas anders angegangen: Wenn in jedem einzelnen Produktionsabschnitt verstanden wird, wie es zu einem qualitativ hochwertigen Ergebnis kommt, können schließlich auch Qualitätssteigerungen für die gesamte Produktionskette erreicht werden.
Einbindung bestehender Systeme
Eine vollständige Automatisierung einer Produktion setzt in der Regel bei der herkömmlichen Produktion an. Im Unterschied zur letzteren erfolgt die Steuerung der Produktionsprozesse bei der vollständig autonomen Fertigung jedoch verstärkt über die erhobenen Produktions- und Qualitätsdaten, denn nur so lassen sich die gewünschten Qualitätssteigerungen erreichen. Ausgangspunkt für eine vollständig autonome Fertigung ist also meist eine traditionelle Produktion mit manuellen Teilschritten. Allerdings ist auch der Aufbau einer neuen Produktionsstätte denkbar, in der von Anfang an ausschließlich vollständig automatisierte Fertigungsprozesse zum Einsatz kommen. Schließlich setzt diese lediglich einen umfangreichen Datensatz voraus, mit dem sich alle Produktionsprozesse hinreichend genau beschreiben lassen.
Von rein reaktiven KI-Systemen hin zu präskriptiven KI-Anwendungen
Ein reaktives KI-System entdeckt einen Qualitätsfehler oft erst am Ende der gesamten Produktionskette. Anschließend reagieren die Produktionsmitarbeiter und nehmen eine Reihe von Änderungen am System vor, um den Fehler für folgende Produktionszyklen zu korrigieren. Dieser Ansatz ist aus zwei Gründen problematisch: Erstens können die Mitarbeiter erst aktiv werden, wenn ein Fehler aufgetreten ist. Zweitens werden solange Waren minderwertiger Qualität produziert, bis die Fehlerursache behoben wurde. Ein präskriptives KI-System funktioniert ganz anders: Hier geht es immer darum, jetzt eine kleine Änderung vorzunehmen, um in Zukunft Qualitätsmängel vermeiden zu können. Allein aufgrund der zu erwartenden Qualitätseinbußen werden also bereits einige Korrekturmaßnahmen angeordnet, um so die Kosten für Ausschuss, Umprogrammierung usw. zu reduzieren. Kommt ein reaktives KI-System zum Einsatz, wird hingegen abgewartet, bis ein Problem auftritt und dadurch Kosten entstehen, bevor korrigierend eingegriffen wird.
Bewährte Maßnahmen für die Umstellung auf die vollständig autonome Fertigung
Folgende zwei Maßnahmen sollten Hersteller ergreifen, um ihr Unternehmen auf die Umstellung auf die vollständig autonome Produktion vorzubereiten:
Produktionsdaten erheben und speichern. Sobald in einer Fertigung Produktionsdaten erhoben und gespeichert werden, können diese auch für Optimierungsprozesse genutzt werden. Das ist das Wichtigste, was Hersteller für die Umstellung auf die vollständig autonome Fertigung zum jetzigen Zeitpunkt tun können, wenn sie noch nicht damit begonnen haben. Das Qualitätssystem verbessern¤ Wenn die Qualität verbessert werden soll, müssen alle Daten etwaiger Fehler genau aufgezeichnet werden (Art, Entstehungsort und genaue Beschreibung). Die alleinige Feststellung, dass ein Fehler aufgetreten ist, reicht nicht aus. Nur so kann das KI-System die Problemursache selbstständig erkennen und entsprechende Anweisungen für die Maschine oder den Bediener daraus ableiten. Dies führt letztlich zu einer Qualitätssteigerung.
DataProphet ist ein weltweit führender Anbieter von künstlicher Intelligenz (KI) für die Fertigung. Unsere preisgekrönte Technologie beinhaltet einzigartige Anpassungen und Weiterentwicklungen des Deep Learning, so dass die KI einen signifikanten, praktischen Einfluss auf die Produktion ausüben kann. Die Lösungen von DataProphet sind so konzipiert, dass sie angepasst und in bestehende Umgebungen integriert werden können, so dass unser Team für digitale Transformation Ihren Betrieb von Null auf KI umstellen kann. Wir verstehen die Fertigung und, dass die tatsächlichen Auswirkungen durch vorbeugende Maßnahmen erreicht werden, da die Echtzeit oft zu spät ist…. Weitere Informationen finden Sie unter www.dataprophet.com
DataProphet
64319 Pfungstadt
Telefon: +49 (6157) 9149272
http://dataprophet.com/
MEPAX
Telefon: +34 (633) 07-94
E-Mail: o.prearo@mepax.com