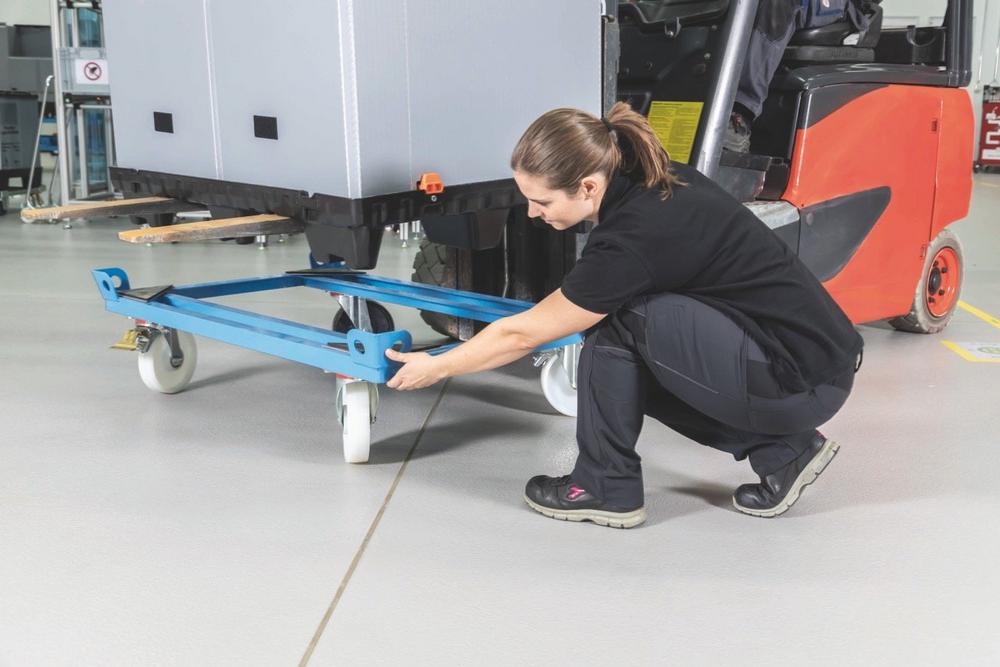
Grundsätzlich gibt es sechs Methoden, einen Bodenroller ruhig zu stellen. Die simpelste heißt, ihn einfach festzuhalten. Dabei handelt es sich gleichzeitig um die mit Abstand schlechteste Art und Weise. Die Werkerin beziehungsweise der Werker würde zu großen Risiken ausgesetzt. Selbst wenn es mal schnell gehen soll – so lieber nicht!
Die nächste Technik besteht darin, die Feststeller zu benutzen. Ein in der Praxis selten beschrittener Weg; schließlich bedeutet er für das Personal einen signifikanten zeitlichen Mehraufwand. Zumal die Bremsvorrichtungen oft an diagonal gegenüberliegenden Rollen sitzen und man um das Fahrgestell herumgehen müsste. Die filigranen Hebelchen sind gelegentlich auch schlecht zu bedienen und entsprechend unbeliebt.
Möglichkeit Nummer drei ist, den Trolley für den Verladeprozess gleich im Routenzug zu belassen. Dadurch wird der Rolluntersetzer sicher in Position gehalten. Obendrein entfällt der Aufwand, ihn anderswohin zu führen. Beide Pluspunkte bringen jedoch Nachteile an anderer Stelle mit sich. Zum einen verlängern sich damit die Standzeiten von Shuttle und Fahrer. Zum anderen nimmt man den Fahrgestellen ihre Pufferfunktion.
Bodenschienen, Magnete oder …
Bodenschienen stellen die vierte Alternative dar. Sie blockieren zumindest zwei von vier Himmelsrichtungen. Ihr großes Manko liegt in den seitlichen Kräften, die mit jedem Beladevorgang dem Bodenroller zusetzen. Aufgrund dessen können die Räder brechen und nennenswerte Personen- und Sachschäden verursachen. Als weitere systemische Schwäche ist der menschliche Energiemehraufwand zu nennen, den einige Fabrikate abverlangen. Das Hinaufschieben auf manche Laufschiene kostet nämlich unnötigen Einsatz – gerade bei schwerer Zuladung. Hinzu kommt das Einfädeln in die vorgegebene Spur, das dann und wann zum Geduldsspiel mutiert.
Magnete bieten eine zusätzliche, fünfte Option. Sie lassen sich beispielsweise an handelsüblichen Sicherheitsbarrieren montieren. Das verleiht dem Trolley wenigstens auf einer Seite Halt. Die Vorteile dieser Vorgehensweise sind offensichtlich. Einerseits entsteht eine physische Sperre zwischen der Staplerzone und dem Routenzugbereich. Was wiederum die Sicherheit der Beschäftigten optimiert. Andererseits braucht der Rolluntersetzer nicht erst zeitraubend platziert zu werden. Doch diesem Aspekt wohnt eine Kehrseite inne. Diese variable Positionierung beraubt den Staplerfahrer um die Wiederholgenauigkeit von Fahrmanövern. Ausschlaggebend ist darüber hinaus die Anziehungskraft der Magneten. Fällt sie zu schwach aus, vermögen sie die Fahrgestelle nur schwer zu bändigen; gerät sie zu stark, so muss das Personal zum Abtransport der Bodenroller zu viel Energie aufwenden.
… die Trolleydockingstation
Bleibt noch die sechste und letzte Methode: die Trolleydockingstation von MWB. Hier fixiert ein leistungsfähiger Mechanismus das mobile Förderhilfsmittel. Das Produktseinerseits wird fest im Boden verankert. Es schafft damit eine massive Sicherheitsbarriere und schottet Fußgänger völlig vom Staplerverkehr ab.
Die Lösung gestattet es, Rolluntersetzer leicht zu be- und entladen – ohne dass dazu ein zweiter Mitarbeiter benötigt würde. Das spart Geld und minimiert die Verletzungsgefahren. Für die Anschaffung der Trolleydockingstation spricht auch, dass sie Verladevorgänge erheblich beschleunigt. Denn mit ihr befinden sich die Rolluntersetzer stets an der wieder und wieder gleichen Stelle. Das hilft erstens Beschäftigten, gesunde Routinen zu entwickeln und vereinfacht die Abläufe. Zweitens ist die Trolleydockingstation somit beim Beladen von fahrerlosen Transportfahrzeugen sehr nützlich.
Als besonders sinnvoll hat sich die Installation mehrerer solcher Stationen erwiesen. Daraus erwächst eine wichtige Pufferzone. Sie ermöglicht es dem Lenker des Routenzugs, gleich nach dem Eintreffen im Supermarkt loszulegen. Den Tausch leerer gegen volle Behälter erledigt er damit autonom – ohne auf die Interaktion mit dem Staplerfahrer angewiesen zu sein. Diese Entkopplung von Prozessen trägt entschieden dazu bei, Ressourcen nachhaltiger einzusetzen.
Zusätzliche Informationen zur Trolleydockingstationstehen auf www.mwbgmbh.de zur Verfügung.
Der Fokus der M.W.B. GmbH liegt auf intralogistischen Speziallösungen. Die Gesellschaft bietet insbesondere Anlagen zum Be- und Entladen von Routenzügen und Trolleys sowie für Handling und Lagerung von Trolleys. Die Sparte Hafenlogistik mit der Marke „Sort + Store“ rundet das Portfolio ab. Das Unternehmen bedient renommierte Kunden auf allen Kontinenten, darunter BMW, DP World, HHLA, Krones, Liebherr, Maersk, Still, Volkswagen, ZF Friedrichshafen und die ZKW Group. Der Mittelständler entwickelt und produziert am Unternehmenssitz im bayerischen Eching. Diplom-Betriebswirt Fritz Merk steuert die Firma seit Gründung im Jahr 2004 als geschäftsführender Gesellschafter; technischer Leiter ist der Maschinenbauingenieur Matthias Huber. Seit 2015 tragen MWB und der Kooperationspartner Cargobeamer den begehrten Titel „Nominated Supplier”, verliehen vom VW-Konzern.
MWB GmbH
Bichlmannstrasse 14
84174 Eching
Telefon: +49 (8709) 92778-0
Telefax: +49 (8709) 92778-100
http://www.mwbgmbh.de
Telefon: +49 / 87 09 / 9 27 78 – 0
Fax: +49 / 87 09 / 9 27 78 – 100
E-Mail: info@mwbgmbh.de